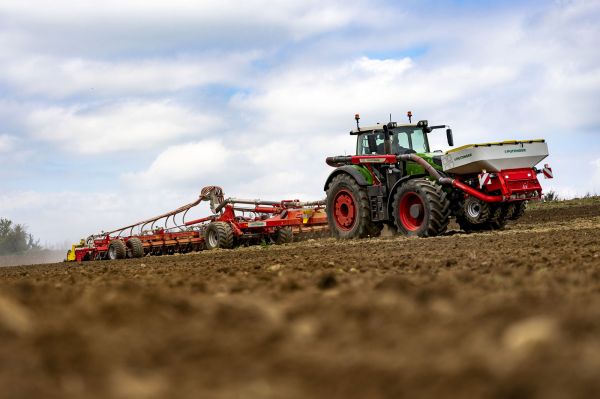
Now, according to the company, soil cultivation and sowing or fertilisation can be done at the same time.
In just one pass, fertiliser or cover crops are sown directly into the soil using this resource-saving process. By feeding fertiliser into the raised flow of soil, it is mixed in and covered straight away. The fertiliser does not lose any of its effectiveness and is immediately available for the plants. This process is suitable for seedbed preparation in spring or for replenishing nutrients with granular trace elements in autumn.
Cover crops are directly stimulated to germinate because they are immediately covered and consolidated by the packer, according to Pöttinger. This can be done during shallow stubble cultivation. Driving speeds above 10km/h in combination with the wide working widths of 8m and 10m ensure an enormous output.
Large, scalloped discs with a diameter of 580mm slice into the ground and get the soil moving. The aggressive setting of the tools ensures reliable soil entry, even in the driest conditions. The Twin Arm suspension system prevents the discs from deviating sideways on hard ground. This ensures that the whole surface is moved, which ultimately ensures uniform application of the seed material and fertiliser.
Setting the distribution rail with the outlet diagonal to the ground feeds the fertiliser or seed into the flow of soil. As a result, the material joins the flow of soil to be deposited on or near the surface. This method is suitable for sowing greening or cover crop mixtures.
By setting the distribution rail perpendicular to the ground, the material is immediately mixed into the soil below so that it is deposited across the full cultivation depth. The fertiliser and seed material is therefore distributed throughout the entire cross section or soil movement. During stubble cultivation, for example, compensatory fertilisation of potash or nitrogen can be used to accelerate the decomposition of straw.
The capacity of 1,700L or 2,400L and a division of 60:40 ensures a wide range of applications for the front hopper. To ensure convenient operation, the Amico front hopper is equipped with Isobus, as standard. The material is applied using a single shoot process with a pressurised hopper system. One or two metering units can be controlled site-specifically by the intelligent control system. Furthermore, the hopper can also be used in combination with third-party equipment thanks to the Isobus control system without any issues.