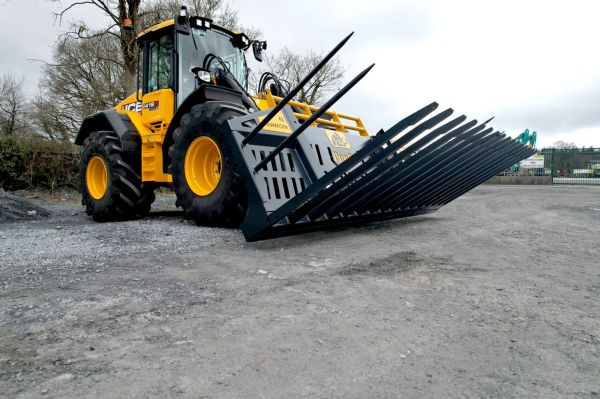
In 2022, the company decided to completely redevelop its ever-popular folding-fork range with a particular focus on strength, performance, and weight after listening to the demands of the modern-day silage contractor. Fast-forward to spring 2023 and the Mammoth and Taurus ranges of folding forks are born and ready for action, according to the company.
Available in widths starting from 3.6m up to an impressive 5.5m and with weights from 1.5-2.2t, there is a model to suit all customers and their machines performance. At the business end, the popular 50mm Hardox tines have been increased to 6ft (1,829mm) with an option for 7ft (2,090mm) tines for larger machines enabling them to carry even more material in one pass. Twin high tensile side tines are bolted in place rather than welded for ease of replacement in the event of damage. For safety, the maximum width when folded in transport position is 2.9m regardless of the forks' working width and for added road safety an optional tine guard can be fitted.
Up top, the spill frame is bolted to the top frame and has been beefed up in line with the rest of the fork, a removable centre section is standard for machines with Z-bar linkage systems, while the entire spill frame can be easily removed for use in low-roof situations.
The folding sides now feature an adjustable wing locking system for added strength and support even in the most demanding applications. Each wing is hydraulically held in place with an added double pilot check valve safety system to prevent creep during operation while also protecting against a wing falling during transport in the event of a hydraulic hose failure. Greaseable 40mm pins are fitted to the double clevis ram ends with 40mm x 50mm replaceable bushings aiding efficiency. The main pivot pins have been enhanced up to massive 80mm x 496mm versions, which again are greaseable and feature replaceable bushings to maximise performance and longevity.
The new bottom section is constructed from high yield 12mm folded and fabricated plates with an added 12mm Hardox wear strip fitted along the bottom to increase wear and improve component life. An angled plate is now fitted to the top of the entire beam both front and back to prevent material retention while also helping material flow through
the fork.