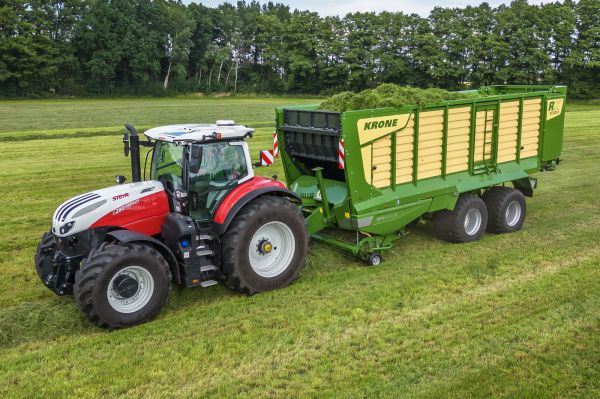
Included on both wagons is the new OptiGrass 28 and 37 cutting system. This new technology allows the incoming grass to be cut to the shortest lengths possible producing feed of the highest quality," the company says.
Integral rotor with SplitCut
Central to the new OptiGrass 28 and 37 cutting system is the integral rotor that distributes the grass evenly across the full cutting width. Measuring 88cm in diameter, this rotor is capable of handling heavy crops at high speeds making it a great choice for contractors. The knife blades on the rotor cutter are arranged on the sides of the feeding plates, making perfect scissor-like cuts without squeezing the grass, a technique that is gentle on the crop and economical. Depending on the size of the cutting system, the feed plates are 17mm or 22mm wide and all are made from high-tensile steel for heavy-duty and long-lasting performance. The incoming grass is reliably fed to the middle of the rotor by 22cm long augers out on the ends of the integral rotor. Krone SplitCut splits the grass flow on the outboard knife blade, and feed tines reverse the flow which is then guided to the middle of the rotor by deflector plates for cutting. These features ensure optimum chopping capacity across the full working width ensuring not a single blade of grass enters the wagon uncut.
OptiGrass for finest cuts
The new high-capacity cutting system is available in two versions – the OptiGrass 37 with 40 blades and nominal cuts of up to 37mm and the OptiGrass 28 with 54 blades for a nominal chopping length of up to 28mm, which is the ideal length for wet silage. In addition, the OptiGrass cutting system with its scissor-like precision not only produces quality feed but also provides an unprecedented level of operator comfort. Potential blockages are removed by dropping the knife bank hydraulically and then raising it again after the blockage is removed. The knife bank also pulls out to the left side for convenient replacement of the individually overload protected blades. All blades are released from a central lever and replaced without the need of tools.
The perfect driveline
The wide rotor is powered by an in-board planetary gearbox and a PowerBelt for maximum output. This PowerBelt on the RX transmits about 25 per cent higher PTO revolutions per minute (RPM) compared with the predecessor. On the ZX, the PTO power flow has increased by up to 10per cent. The belt drive concept ensures optimised performance with less wear and lower maintenance requirements while the increase in speed reduces lower power requirements, operating more efficiently while reducing component wear. Another new feature unique to Krone are the two interchangeable pulleys. These can be swapped easily and quickly to adjust the processing speed, allowing the wagon to adapt to varying harvest conditions while still ensuring the space behind the rotor is always loaded to capacity for high pre-compression and the best possible cutting quality.
Great ride comfort in any terrain
The RX and ZX models run on tandem or tridem axles that distribute the weight uniformly to all wheels, making them stable and comfortable to drive as well as protecting the ground. The new articulated drawbar with hydraulic height control and standard suspension also improved driver comfort. Slim and compact, the bar makes for excellent operator visibility of the pick-up and enhanced maneuverability. In combination with the intelligent caster-steer axle and the optional and contactless electronic forced steering system, the ground is protected and tyre wear is minimised.
Large choice of options
Various options such as crop covers, a weighing system and the integral silage additive applicator with a 200L tank and four flat fan nozzles on the pick-up or rotor cutter are available. The new electronic filling level sensor, which is standard specification, monitors the filling level by measuring the advance of the chain-and-slat floor and displaying the reading on the terminal on a scale from 0 to 100.
All machines come with software that allows operators to customize the lubrication intervals for the central lubricator. On top of this, there is a standard premium LED lighting kit which lights the vicinity, the crop flow system, the load space and the lubrication points. As for control units, the ZX and RX models are available with a variety of control units, ranging from the DS 100 head unit to the premium-level Isobus CCI 800 and 1200 terminals that provide intuitive user interface.